Versatile Applications of Compressed Knitted Wire Mesh in the Automotive Industry
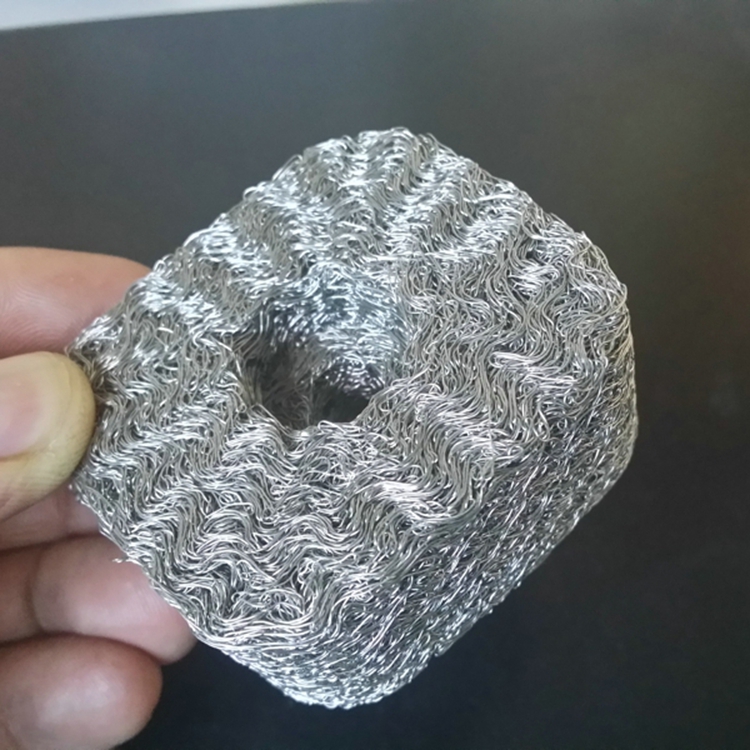
In the automotive industry, compressed knitted wire mesh finds various applications. Here are some common examples:
Exhaust system: Compressed knitted wire mesh is used to manufacture automotive exhaust system components, such as catalytic converters and exhaust mufflers. They help reduce tailpipe emissions and filter out harmful gases.
Gaskets: Compressed knitted wire mesh can be used as gaskets for automotive engines, transmission systems, and other critical components. They provide excellent sealing performance, ensuring that liquids and gases do not leak.
Liquid filters: Compressed knitted wire mesh is employed as the filter element in automotive liquid filters. They effectively filter engine oil, fuel, coolant, and other fluids, preventing impurities and particles from entering the engine and other critical systems.
Air filters: In the automotive air intake system, compressed knitted wire mesh is used to manufacture air filters. This helps prevent dust, insects, and other contaminants from entering the engine, maintaining optimal engine performance.
Hydraulic systems: Compressed knitted wire mesh finds applications in automotive hydraulic systems, used for manufacturing hydraulic seals and dampers.
EMI/RFI shielding: Compressed knitted wire mesh is utilized in automotive electronics and communication systems to provide electromagnetic interference (EMI) and radio-frequency interference (RFI) shielding, ensuring system stability and reliability.
Fuel systems: In automotive fuel systems, compressed knitted wire mesh is used to manufacture fuel filters, effectively filtering impurities in the fuel and protecting fuel injectors and other crucial components.
These are some common applications of compressed knitted wire mesh in the automotive industry. Due to its outstanding performance and versatility, this material plays a vital role in automotive manufacturing and maintenance.